Banton frameworks INTERVIEW
The making of handcrafted sunglasses
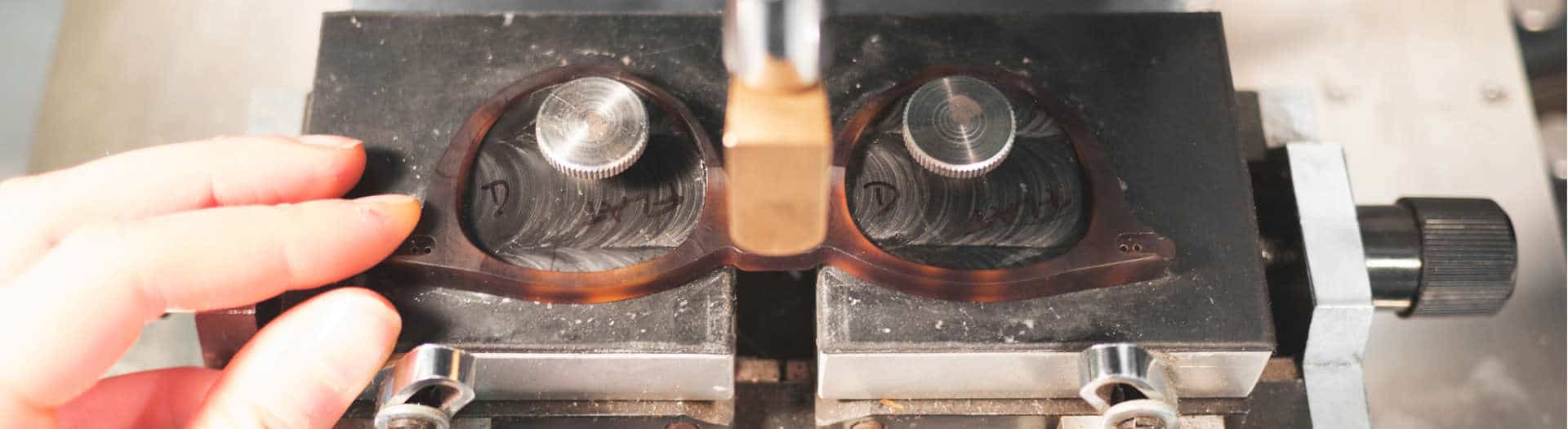
Lucy Ross and Jamie Bartlett, the founders of Banton Frameworks are the guinea pigs for our first behind the scenes interviews. Sir Gordon Bennett is on a mission to showcase and help keep British craftsmanship alive. And what better way than showing you behind the scenes. Uncovering why buying better products are worth every penny. The art and graft that goes into these products speaks for themselves when you own them, but sometimes taking a voyeuristic journey makes them even more of a joy to own. As you begin to understand the method and dedication that goes into creating objects that will last, your appreciation will grow too.
So welcome Lucy and Jamie to the Banton Frameworks interview. Thank you for agreeing to bear you maker soul to SirGordonBennett.
Let's start with the easy stuff. Lucy, what inspired you to start Banton Frameworks?
Lucy: It began as my final year university project back in 2012. I was intrigued by eyewear and the effect it had on a person’s perception. Studying Product Design and as a glasses wearer myself, I began prototyping my own frames.
Graduation came and went, but I was still dabbling with frame-making. By this point my coursemate, now partner, Jamie had joined-in. We both became infatuated with learning how to make glasses so we kept using the university equipment and workshop machinery.
Over the summer, after having graduated, we then started breaking back into university workshop at night to continue with our new optical obsession. It was literally our second education, one that’s continuing to this day...but just in our own workshop now and not in twilight hours.
SGB: With that in mind, how did you go about getting Banton Frameworks off the ground?
Lucy: Our ‘night classes’ using the old university equipment paid off. Over the summer, we’d made enough parts of glasses frames to take to London Design week that September. During the design week, we hosted a live frame-assembly pop-up and sold just enough frames to get ourselves home and buy our first workshop machine.
From there, we made more glasses. We sold them. We bought another machine.
And that’s pretty much it. Making, learning, selling, more making. It’s been nearly a decade of continual research and development. Still going strong.
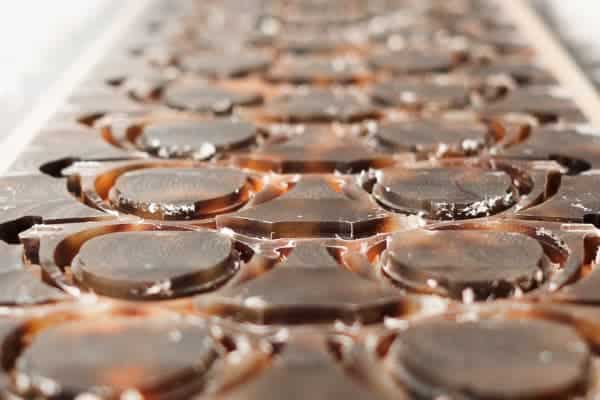
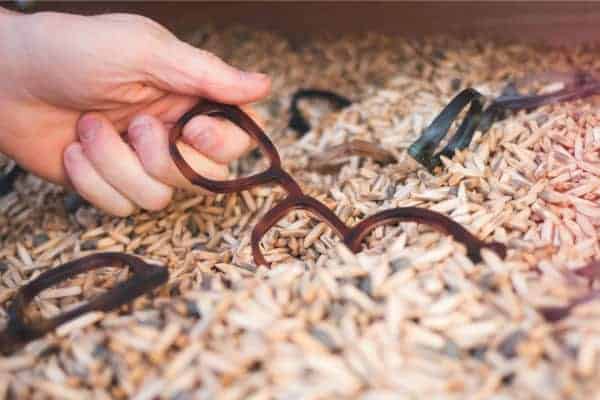
SGB: How many designs did you create until you found the final shape and materials of your sunglasses?
Jamie: In the early days, 2012 - 2015, we had a box of “f*ck up frames.” Regularly, we’d fling broken or incorrect frames across our workshop into the box. I’d say we made at least 2 or 3 thousand frames before things started going right. Honestly, looking back, we were mad.
And yes, in case you were wondering, we kept quite a few of them for old time’s sake. But now, it’s called ‘the memories box.’
SGB: What is a typical day in the Banton Frameworks workshop?
Jamie: Things have changed dramatically over the years. Before we’d make tiny batches of a handful of frames. More than 10 would be max-capacity 12 hour days haha. However, these days because of our machinery investments and efficiency, we work in much larger batches of a 100 or so. This means we tend to work in intensive cycles where we spend about 2 weeks at a time purely making. You’ll be able to tell when this happens by the slow email response rate.
SGB: Can you walk us through the process of making sunglasses?
Lucy: Sure, so we start by cutting sheets of acetate into strips using a circular saw so they can fit inside our CNC machine. Then the strips are clamped and secured inside the machine and cut into frame fronts.
Jamie: Afterwards, we locate the steel rivets through the temples and frame fronts using what’s called a staking tool. This pushes the rivets through the acetate before we overlay the hinges.
The hinges are then permanently attached to the frame using a pneumatic riveting tool. This is the traditional method and creates a solid fixture which can also be repaired after years of use. It takes a while to do this as you have to rivet all 8 rivets separately for each frame. 4 for the temples and 4 for the frame fronts.
Lucy: After that, the frame fronts and temples are individually heated and formed using specific tooling to give their correct shape.
Jamie: Next is tumble polishing. Our new tumbling machine holds about 500 frames in four separate chambers full of wooden chips. This tosses the frame fronts and temples around to remove their sharp/rough edges from machining. This process takes about 72-96 hours, continually, non-stop.
Lucy: After 4 days of tumble polishing, we then hand polish each frame front. This is done using 4 grades of progressively fine paste to achieve an immaculate shine. This is very labour intensive, but it gives our frames an incredible lustre. It’s a very addictive process.
Jamie: We then assemble the frames and asses them dimensionally to check if they require any adjustments before lens fitting.
Lucy: Finally we fit our premium polarised lenses These are specifically designed to reduce the effects of glare and have a special anti-reflective coating on the rear-side. They’re our best sunglasses lenses yet!
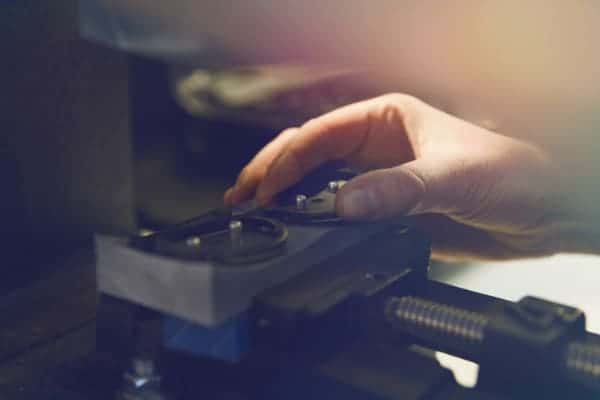
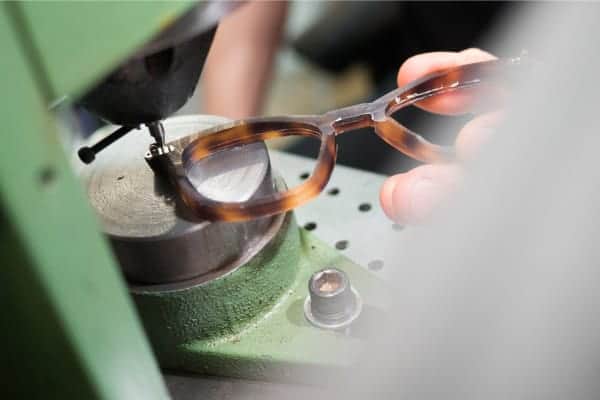
SGB: What is the most satisfying part of the process?
Jamie: Hmmm, for me it’s probably riveting. That’s one of my specific jobs and is something I take a lot of pride in doing.
Lucy: Definitely tumble polishing. It’s a hands-off once they’re being polished inside the drums, but it makes the frames come to life and really makes the acetate sing.
SGB: What is your personal favourite tool in your arsenal?
Jamie: My pneumatic riveting machine. We imported it all the way from America and it’s easily the most attractive machine we own. It was made in 1976 and makes a beautiful noise when it forms each rivet. Clunk.
Lucy: My CNC machine. It’s so accurate and means I can control every aspect of the cutting, sculpting and shaping of each frame. Geek level: 100
SGB: What details of your sunglasses make them special?
Jamie: When you get them in your hands you’ll know. “They feel so solid” is one of our most common comments. Makes me smile every time I hear that.
SGB: What craftsmanship methods do you utilise to achieve this?
Lucy: It’s a combination of a women, a man and some very specific machines. Because we’re a manufacturer, we use machinery and automation to help us work at higher volumes. But, there is a lot of skill in the use of these machines and the manual processes in-between.
Jamie: Riveting takes so much concentration. One mistake and it’s game over. Same goes for hand polishing. You have to really know what you’re doing, how much pressure to apply, don’t let the acetate get hot and when to change polishing compounds.
Lucy: Adjusting frames so they sit level, so they can take a lens; that takes so much practice. Especially at volume. There are no shortcuts to quality.
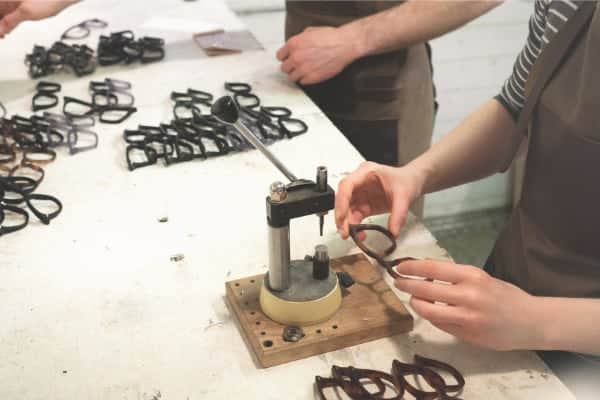
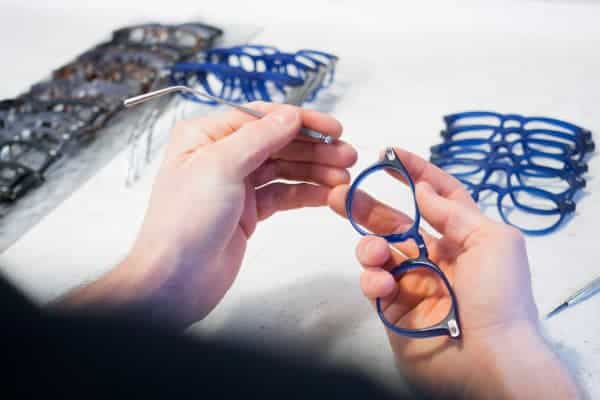
SGB: When it comes to inspiration what makes you want to create?
Jamie: Buying, owning and using things of good quality. When you cherish and own something that’s really well made, it’s such an important reminder that throw-away items are such a false economy. Buy less, buy better.
SGB: Do you have any brands, designers or makers that inspire you?
Lucy: I’ve always loved Vitsœ, ever since I was in University. I’m also a big fan of Ajoto who made my incredible pen.
Jamie: Love Loake shoes. Hiut denim jeans. Trakke bags. Alice Made This. The guys at Paynter Jacket Co. do a great job also.
SGB: How do you make the Loch Banton workshop an inspiring place to work? (Not including your workshop being located on a Loch in Scotland)
Lucy: Funnily enough, we don’t dress it up too much. We’re both very tidy and organised but because it’s a workshop, there isn’t much ornamentation. Mostly, we’re driven by our purpose to make exceptionally good eyewear. That’s our biggest push.
SGB: How do you want people to feel when they wear your sunglasses?
Jamie: Special. Well-considered. Classic.
SGB: Without giving away any state secret, can you let us into any future plans for Banton Frameworks?
Lucy: Big plans for 2020/2021. More new machines are on their way to our workshop which is going to revolutionise how we manufacture. It’s taken us 8 years to get here and it feels like we’re only just getting started. For us, we’ve always been striving to make the best frames we possibly can and I think our goal to become a leading Scottish/UK manufacturer is within our sights.
Building an eyewear factory beside a loch in Scotland.
SGB: Thank you Lucy and Jamie for some splendid insights into what goes into making a pair of handcrafted sunglasses. It really is art and graft all rolled into one. We are super proud to help support your business and grow with you. I can hear 'Hear come the sun' in our head now. Cheers.
If you fancy standing out from the boring RayBan crowd click on the images below for some perfect unisex sunglasses, hand crafted in Scotland.
And you can follow Banton Frameworks on Instagram by clicking here.
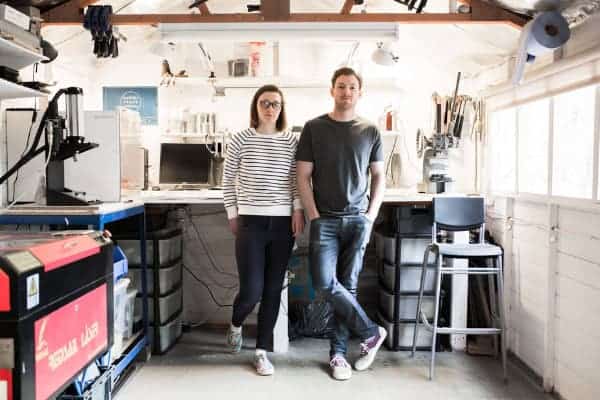
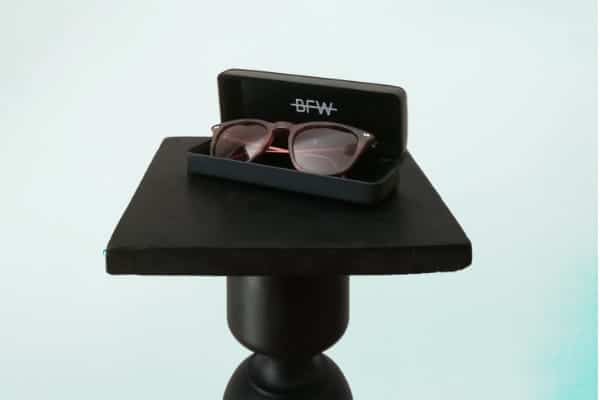